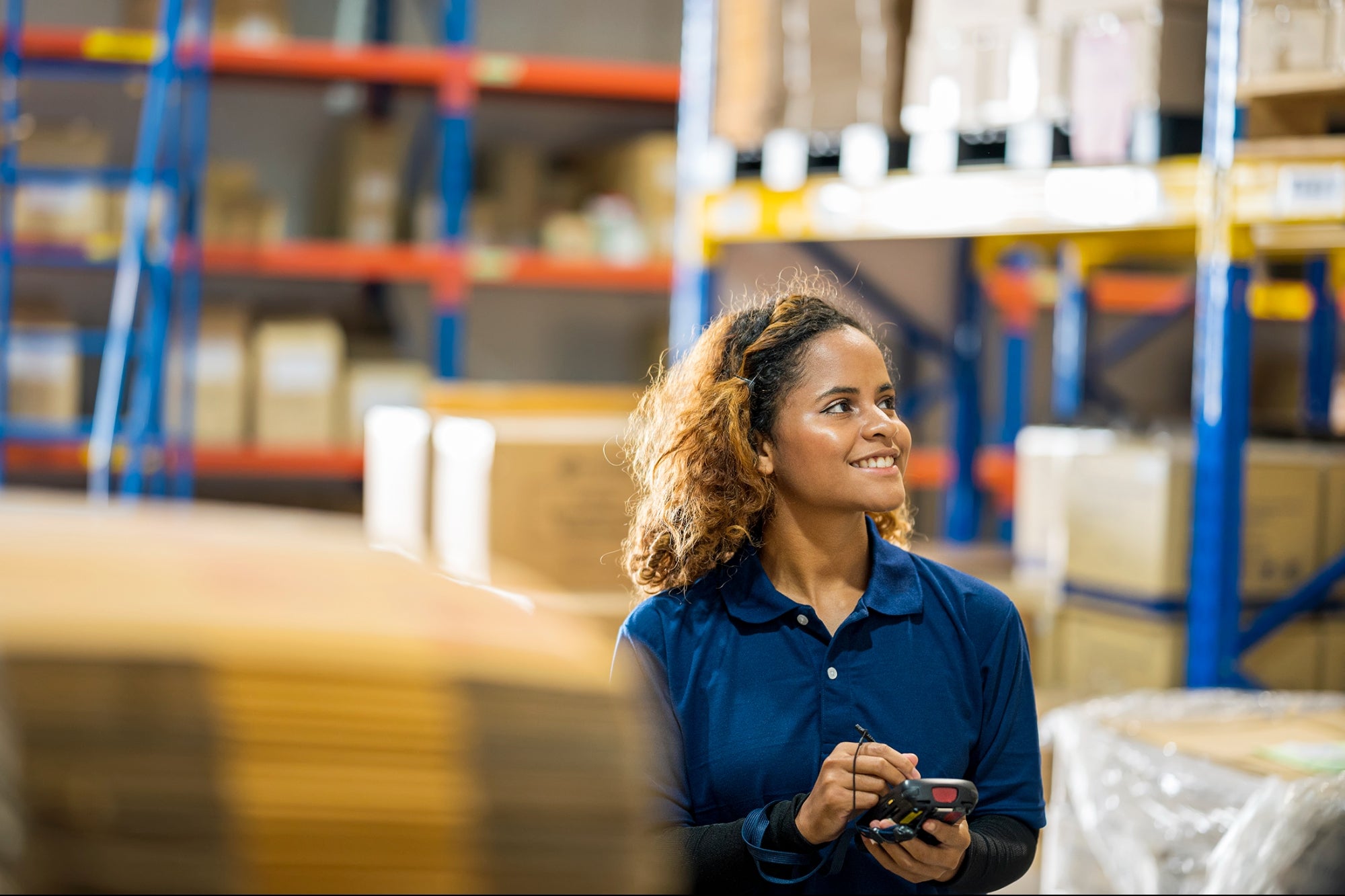
Opinions expressed by Entrepreneur contributors are their own.
Labor shortages across the U.S. are impacting businesses of every size across all industries, with a whopping 9.9 million job openings and only 5.8 million unemployed workers available to fill the roles, according to the latest data from the U.S. Chamber of Commerce. While many factors are contributing to the labor shortage, at the heart, the problem is structural, with declining U.S. birth rates and the drop in net immigration resulting in a lack of available workers.
Warehouse operations have been hit particularly hard by the labor shortage, complicated further by the extremely high turnover rate in the industry. According to the U.S. Bureau of Labor Statistics (BLS), 216,000 people in the transportation and warehouse industry quit their job in April 2023. With 351,000 hires in the month, this exodus translates to a 3% quit rate, second only to the retail (3.5%) and leisure and hospitality (4.6%) sectors. Figures like these shine a spotlight on the retention and hiring challenges that business leaders across industries are facing.
Related: The Labor Shortage Is Only Getting Worse. What’s Causing It and How Can I Avoid Losing Staff?
Focus on happy teams
In light of the labor supply/demand imbalance and the potentially crippling impact of peak season volumes on warehouse teams already stretched to the limit, meeting the demands of fulfillment operations is dependent on retaining quality workers. But employee retention is a significant hurdle, with an abundance of warehouse vacancies available across multiple industries and low barriers of entry for dissatisfied workers looking to change jobs. How can business leaders cope with this revolving door?
Keeping existing warehouse staff happy with less stress and friction in their workday is fundamental to retailers’ retention efforts. While labor shortages are forcing organizations to do more with less in the warehouse, streamlining fulfillment workflows to increase efficiency and productivity, savvy business leaders are also looking at ways to optimize warehouse operations with the employee experience in mind.
By leveraging warehouse management technology to simplify and expedite fulfillment tasks, companies can prevent workload overwhelm, reduce stress and improve job satisfaction for their warehouse teams which, in turn, helps to build loyalty and reduce employee churn.
Related: 4 Ways to Boost Your Employee Retention in an Uncertain Economy
Simplifying with tech
While shipping the right items in the right quantities to the right customer may seem like a no-brainer from the outside looking in, warehouse teams relying on manual, paper-based practices are up against a wall. Given that one of the most common complaints of warehouse workers is unmanageable workloads, it’s a smart strategy to leverage technology that helps employees alleviate workplace stress by completing tasks faster yet with less effort.
In addition to enabling more efficient workflows to boost fulfillment capacity, the aim of warehouse management systems (WMS) is to simplify and accelerate employees’ day-to-day tasks. When it comes to receiving, merchants without a WMS typically rely on specific staff to determine where to put inventory, which means that, oftentimes, the broader warehouse team does not always know where exactly to go (e.g. floor/area/aisle/shelf/bin) to find what they need for an order.
With WMS technology that supports barcode scanning, inventory can be registered quickly into locations by scanning the location and the item. Barcoded items can be easily moved to new locations by scanning the item or selecting all items in the location. Armed with a barcode scanner and mobile app — instead of a clipboard — warehouse workers receive a digital pick list and follow guided optimized walking paths throughout the warehouse. Given they can walk several miles every day, reducing “mileage” makes the job easier and less physically taxing.
In addition, tech-enabled pick methods (e.g. single item batch picking, pick and sort to trolley, multiple orders by item) enable workers to easily handle more volume, faster; for example, multi-order picking can decrease walk time by 85% compared to single order picking.
Related: Using Tech to Build Supply Chain Resilience in a Changing World
Job satisfaction linked to better operational metrics
For businesses in diverse industries, adding a WMS to the tech stack is not just a boon for employee satisfaction, it produces substantial gains on the operational front as well. Organizations can manage their warehouse operations in real time, ensure inventory counts are accurate and synced with online storefronts and marketplaces to reduce the risk of overselling and increase fulfillment capacity with more efficient order picking and shipping. The ability to process more orders accurately and efficiently without hiring more people is particularly valuable in light of ongoing staffing challenges, helping to increase profit margins and drive growth.
How business leaders are the gatekeepers to warehouse innovation
For an organization to successfully leverage technology like WMS in the warehouse, top management must realize that supply chain and logistics agility is critical to company performance and take steps to enable innovation.
Indeed, there’s a clear correlation between the strategies and decisions of top financial performers and those companies whose senior management hold the belief that supply chain and logistics innovation is crucial to success versus those whose senior management feels differently. Ultimately, business leaders across industries are the gatekeepers to technology innovation, and supply chain innovation in particular can make or break a company’s bottom line.
This is underscored in the research study Supply Chain and Logistics Innovation Accelerates, but Has a Long Way to Go, which surveyed 1,000 global execs in the supply chain arena: “Respondents who said they were better financial performers were 20% more likely to have senior management who believes innovation is important and 16% more likely to have lower employee turnover.”
In fact, when it comes to warehouse management in particular, 23% of respondents said that WMS technology will be one of the top focus areas for innovation for the next two years.
In light of warehouse worker shortages, leaders need to prioritize the employee experience in the warehouse to ensure workers are happy, healthy and not looking for the door. They can accomplish this goal — and boost the bottom line at the same time — by opening the doors to innovation in their organization and leveraging warehouse management technology in order to streamline, accelerate and simplify order fulfillment operations. Everyone wins!
This article is from Entrepreneur.com